
主1933年(昭和8年)に創業し、今年で83年を迎える。創業時は熱硬化性プラスチック(ベークライト等)の切削加工から始まり、現在では熱可塑性プラスチックの圧空・真空成形加工及び、プラスチック精密切削加工の製造販売に特化。
プラスチック圧空・真空成形品及びプラスチック精密切削加工品の製造販売で多品種少量生産化という、顧客ニーズの実現に協力し事業を継続的に行う。
その中でも、事業の8割を占める医療・分析計測機器分野は、少量生産品が多くプラスチック成形化に遅れていたが、他成形に比べ初期投資費用を抑えることが可能な圧空・真空成形法により、少量生産対応、デザイン性向上や軽量化という顧客ニーズを実現している。
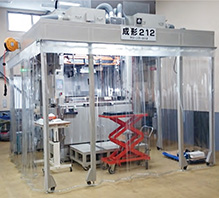
プラスチック成型法の多くは「射出成形法」が用いられている。
これらはペレット状(粒形状)のプラスチック材をヒーターで加熱軟化させ、金型の凸型と凹型の隙間へ高圧を掛けて流し込み冷却して型形状を再現する成形法。そのため金型の費用が高価となり、ある程度多くの成形数量が必要になる。
それに比べ、同社が行っている「真空成形法」は、シート状(厚み2mm〜5mmの板形状)のプラスチック板をヒーターで加熱軟化させ、金型は片側(凸型又は凹型の一方)とプラスチック板の隙間を真空状態にすることで、大気圧がプラスチック板を金型へ押さえつけ、その状態で冷却し型形状を再現する成形法。金型は片側だけなので射出成形に比べ費用が安価なうえ、数量面でも1枚のプラスチック板から成形が可能です。
また「圧空成形法」は、大気圧に加え圧縮空気で押さえつけるので、より型形状の再現性を高めることが出来る。
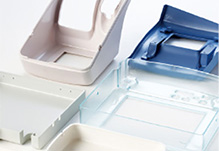
圧空・真空技術を向上させるためには市販の成形機では限界があると判断し、1997年(平成9年)圧空・真空成形機の自社開発に成功。現在まで改良を重ねてきた。
創業80年を超える経験と実績から、圧空・真空成形の特性を生かしたデザインや軽量化(コスト削減)を実現する提案と、3Dデータを効果的に使い試作レスの実績の増加。定期的に展示会に出展し、圧空・真空成形品の知名度アップに繋げている。
自社開発のクリーン省エネ圧空・真空成形機は、多機能な仕様により難易度の高い成形品を実現。市場からも高い評価点を得ている。メイドインジャパンにこだわり、今後もその方針を大切にしていく考え。
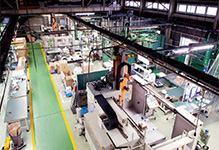
「医療機器用・計測機器用・電子機器用カバー等のプラスチック成形品・加工品の製造」を通して、“多品種少量生産分野の顧客ニーズを実現すること”、そして“かけがえのない自然を後世に残すこと”、を“社会と未来への貢献”であることを使命と捉えて、創意あるプラスチック加工を目指している。
今後の展開は、既存の成形機を、クリーン省エネのハロゲンヒーター搭載の自社開発成形機に置き換えることと、独自の成形シミュレーションソフト導入による肉厚分布予測すること。型当り面“ツヤあり圧空成形品”の製品化も目指す。
株式会社荒木製作所
-
代表取締役社長三原 克敏
- 住所/〒573-1132枚方市招提田近2-2-3
- TEL/0728-67-1721
- FAX/0728-67-1720
- 創業/昭和8年11月
- 設立/昭和36年5月
- 資本金/2,000万円
- 従業員/42人
- HPアドレス/http://www.araki-mfg.com/